Shell molding was developed as a manufacturing process during the mid-20th century in Germany by Johannes Carl Adolf Croning. Shell mold casting is a metal casting process similar to sand casting, in that molten metal is poured into an expendable mold. However, in shell mold casting, the mold is a thin-walled shell created from applying a sand-resin mixture around a pattern. The pattern, a metal piece in the shape of the desired part, is reused to form multiple shell molds. A reusable pattern allows for higher production rates, while the disposable molds enable complex geometries to be cast. Shell mold casting requires the use of a metal pattern, oven, sand-resin mixture, dump box, and molten metal.
Shell mold casting is particularly suitable for castings under 20 lb sand compared to sand casting, this process has better dimensional accuracy, a higher productivity rate, and lower labor requirements. It is used for small to medium parts that require high precision. Almost any metal that can be cast in sand can be cast with the shell molding process. Also much larger parts have been manufactured with shell molding. Typical parts manufactured in industry using the shell mold casting process include transmission connectors, grounding products, aluminium connectors, cable clamps, hot line clamps, cylinder heads, gears, brass nuts, brass washers bushings, connecting rods, camshafts, valve bodies and other casting parts for electric transmission, automobile industry, bathroom fitting hardware, construction and scaffolding industry and marine industry etc.
The Process
The first step in the shell mold casting process is to manufacture the shell mold. The sand we use for the shell molding process is of a much smaller grain size than the typical green sand mold. This fine grained sand is mixed with a thermosetting resin binder. A special metal pattern is coated with a parting agent, (typically silicone), which will latter facilitate in the removal of the shell. The metal pattern is then heated to a temperature of 350F-700F degrees, (175C-370C).
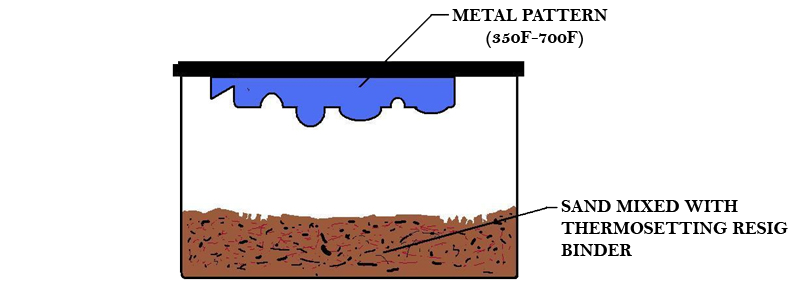
The sand mixture is then poured or blown over the hot casting pattern. Due to the reaction of the thermosetting resin with the hot metal pattern, a thin shell forms on the surface of the pattern. The desired thickness of the shell is dependent upon the strength requirements of the mold for the particular metal casting application. A typical industrial manufacturing mold for a shell molding casting process could be .3in (7.5mm) thick. The thickness of the mold can be controlled by the length of time the sand mixture is in contact with the metal casting pattern.
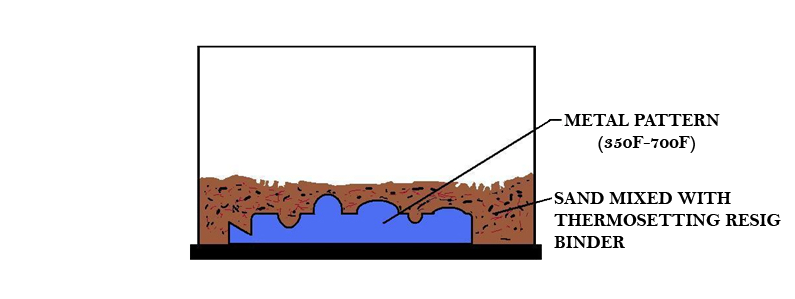
The excess "loose" sand is then removed, leaving the shell and pattern.
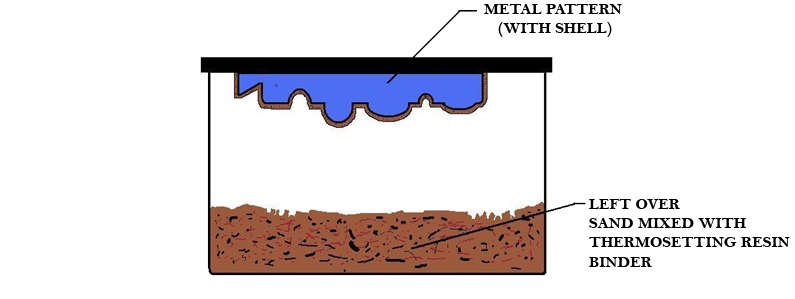
The shell and pattern are then placed in an oven for a short period of time, (minutes), which causes the shell to harden onto the casting pattern.
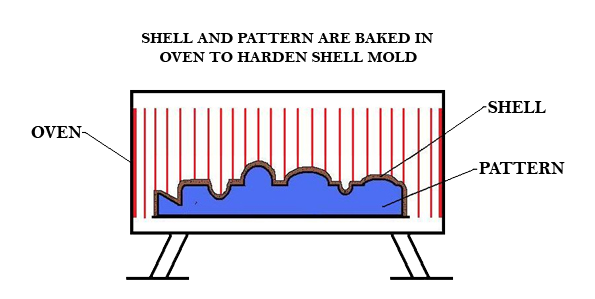
Once the baking phase of the manufacturing process is complete, the hardened shell is separated from the casting pattern by way of ejector pins built into the pattern. It is of note that this manufacturing technique used to create the mold in the shell molding process can also be employed to produced highly accurate fine grained mold cores for other metal casting processes.
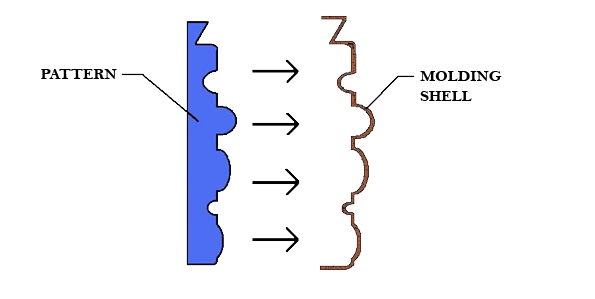
Two of these hardened shells, each representing half the mold for the casting, are assembled together either by gluing or clamping.
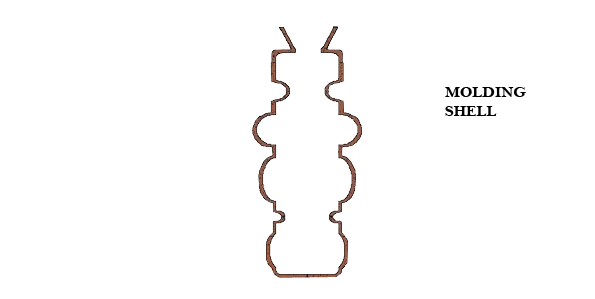
The manufacture of the shell mold is now complete and ready for the pouring of the metal casting. In many shell molding processes, the shell mold is supported by sand or metal shot during the casting process.
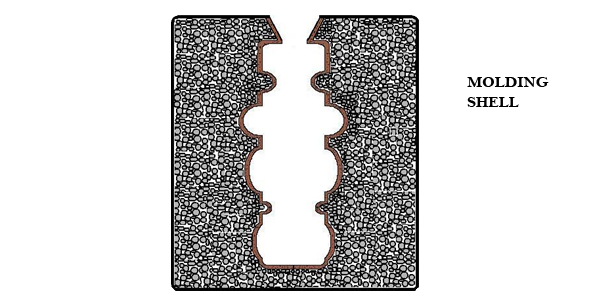
Properties and Considerations of Manufacturing by Shell Mold Casting
- The internal surface of the shell mold is very smooth and rigid. This allows for an easy flow of the liquid metal through the mold cavity during the pouring of the casting, giving castings a very good surface finish. Shell mold casting enables the manufacture of complex parts with thin sections and smaller projections than green sand mold casting.
- Manufacturing with the shell mold process also imparts high dimensional accuracy. Tolerances of .010 inches (.25mm) are possible. Further machining is usually unnecessary when casting by this process.
- Shell sand molds are less permeable than green sand molds and binder may produce a large volume of gas as it contacts the molten metal being poured for the casting. For these reasons, shell molds should be well ventilated.
- The expense of shell mold casting is increased by the cost of the thermosetting resin binder, but decreased by the fact that only a small percentage of sand is used compared to other sand casting processes.
- Shell mold casting processes are easily automated.
- The special metal patterns needed for shell mold casting are expensive, making it a less desirable process for short runs. However, manufacturing by shell casting may be economical for large batch production.